Dicas de construção - Dosagem
Princípios Básicos do Concreto Dosado em Central
1. Concreto Dosado em Central: Benefícios da Opção
Na hora de se construir surge uma grande dúvida: devo utilizar o concreto dosado em central ou "virar" esse concreto na própria obra?
Optar pelo concreto dosado em central proporciona diversas vantagens que são facilmente observadas, entre as quais destacamos:
eliminação das perdas de areia, brita e cimento. Racionalização do número de operários da obra, com conseqüente diminuição dos encargos sociais e trabalhistas. Maior agilidade e produtividade da equipe de trabalho. Garantia da qualidade do concreto graças ao rígido controle adotado pelas centrais dosadoras. Redução no controle de suprimentos, materiais e equipamentos, bem como eliminação das áreas de estoque, com melhor aproveitamento do canteiro de obras. Redução do custo total da obra.
2. Preparação e Cuidados para o Recebimento do Concreto
Na obra, o trajeto a ser percorrido pelo caminhão betoneira até o ponto de descarga do concreto deve estar limpo e ser realizado em terreno firme, evitando, assim, o atolamento e as manobras difíceis que podem atrasar a concretagem em andamento.
A circulação dos caminhões deve ser facilitada, de modo que o caminhão seguinte não impeça a saída do caminhão vazio.
A descarga do concreto deve ocorrer no menor prazo possível; quando for lançado por meio de bombeamento ou quando grande número de caminhões estiver circulando, deve-se prever um local próximo a concretagem para que os caminhões possam aguardar o momento do descarregamento.
Deve-se verificar se a obra dispõe de vibradores suficientes, se os acessos e os equipamentos para o transporte de concreto estão em bom estado - guinchos, carrinhos etc. - e se a equipe operacional está dimensionada para o volume e o prazo de concretagem previsto.
3. Fôrmas, Armaduras e Escoramento
Antes de solicitar o concreto, confira as medidas e a posição das formas, verificando se suas dimensões estão dentro das tolerâncias previstas no projeto. Certifique-se de que estão limpas e de que suas juntas estejam vedadas para evitar a fuga da pasta. As formas e o travamento deverão apresentar rigidez suficiente para resistir a esforços que ocorrem durante o processo de concretagem.
Quanto às formas absorventes, é preciso molhá-las até a saturação antes de aplicar o concreto.
Quando necessitar de desmoldantes, estes devem ser de qualidade tal, que não sejam prejudiciais ao concreto e devem ser aplicados antes da colocação da armadura.
As armaduras devem estar posicionadas de acordo com as especificações do projeto, obedecendo à linearidade e distância entre barras, com espaçadores que garantam os cobrimentos mínimos estabelecidos e ainda garantir que, mesmo em locais de grande concentração, sejam envolvidas pelo concreto.
O escoramento deve ser dimensionado de forma a suportar o peso das formas, ferragens e do concreto a ser aplicado, bem como das cargas que venham a ocorrer durante a concretagem - movimentação de pessoal, transporte do concreto etc. - e ainda impedir deformações que venham a alterar as dimensões da peça recém-concretada.
4. Aditivos para o Concreto
Os aditivos para o concreto permitem melhorar o seu desempenho.
O aditivo plastificante torna o concreto mais trabalhável, facilitando seu adensamento, sendo aconselhável sua utilização em peças esbeltas de difícil concretagem. Proporciona ainda melhor acabamento na superfície concretado.
O aditivo retardador permite aumentar o período de manuseio do concreto, retardando o seu endurecimento e possibilitando seu fornecimento em locais distantes da central dosadora, ou em concretagens demoradas.
Pode-se ainda utilizar um aditivo plastificante e retardador, combinando as duas características descritas acima.
O aditivo impermeabilizante é indicado para caixas d'água, lajes impermeabilizadas, locais com infiltrações etc., melhorando a proteção contra a passagem de água.
5. Pedido e Programação do Concreto
Para solicitar os serviços de uma central dosadora de concreto deve-se ter em mãos todos os dados necessários, tais como:
indicações precisas da localização da obra. O volume calculado medindo-se as formas. A resistência característica do concreto à compressão (fck) que consta do projeto estrutural, ou seu consumo de cimento - quantidade de cimento por m³ de concreto, quando necessário. O tamanho do agregado graúdo a ser utilizado, pedras 1ou 2, em função das dimensões da peça e distância entre armaduras. O abatimento (slump test) adequado ao tipo de peça a ser concretada.
A programação deve incluir também o volume por caminhão a ser entregue, bem como o intervalo de entrega entre caminhões, dimensionado em função da capacidade de aplicação do concreto, pela equipe da obra.
A programação deve ser feita com antecedência, de modo a evitar atrasos, especificando horário de início da concretagem e intervalo de fornecimento.
6. Recebimento do Concreto
Com a chegada do caminhão na obra, antes do descarregamento, deve-se verificar todas as características especificadas no pedido e conseqüentemente no documento de entrega do concreto, que deve conter informações como:
volume do concreto; abatimento (slump test); resistência característica do concreto à compressão (fck) ou o consumo de cimento; aditivo, quando utilizado.
Antes da descarga do caminhão deve-se avaliar se a quantidade de água existente no concreto está compatível com as especificações, não havendo falta ou excesso de água. A falta de água dificulta a aplicação do concreto, criando "nichos" de concretagem, e o excesso de água, embora facilite sua aplicação, diminui consideravelmente sua resistência. Esta avaliação é feita por meio de um ensaio simples, denominado ensaio de abatimento do concreto (slump test).
As regras para a reposição de água perdida por evaporação são especificadas pela norma técnica brasileira NBR 7212-Execução de concreto dosado em central-Procedimento. De uma forma geral, a adição de água permitida não deve ultrapassar a medida do abatimento solicitada pela obra e especificada no documento de entrega do concreto.
7. Ensaio de Abatimento (Slump Test)
A simplicidade do ensaio de abatimento (slump test) o consagrou como o principal controle de recebimento do concreto na obra e, para que ele cumpra este importante papel, é preciso executá-lo corretamente, como a seguir:
colete a amostra de concreto depois de descarregar 0,5 m³ de concreto do caminhão e em volume aproximado de 30 litros; coloque o cone sobre a placa metálica bem nivelada e apóie seus pés sobre as abas inferiores do cone; preencha o cone em 3 camadas iguais e aplique 25 golpes uniformemente distribuídos em cada camada; adense a camada junto à base, de forma que a haste de socamento penetre em toda a espessura. No adensamento-das camadas restantes, a haste deve penetrar até ser atingida a camada inferior adjacente; após a compactação da última camada, retire o excesso de concreto e alise a superfície com uma régua metálica; retire o cone içando-o com cuidado na direção vertical; coloque a haste sobre o cone invertido e meça a distância entre a parte inferior da haste e o ponto médio do concreto, expressando o resultado em milímetros.
8. Amostragem do Concreto
Depois do concreto ser aceito por meio do ensaio de abatimento (slump test), deve-se coletar uma amostra que seja representativa do concreto para o ensaio de resistência.
A retirada de amostras do concreto deve seguir as especificações constantes nas normas brasileiras.
Não é permitido tirar amostras tanto no princípio quanto no final da descarga da betoneira. A amostra deve ser colhida no terço médio da mistura.
A amostra deve ser coletada cortando o fluxo de descarga do concreto, utilizando-se para isso um recipiente ou "carrinho de mão" e, em seguida, remexida para assegurar sua uniformidade.
Retira-se uma quantidade suficiente, 50% maior que o volume necessário, e nunca menor que 30 litros.
A moldagem é descrita a seguir:
preencha os moldes em quatro camadas iguais e sucessivas, aplicando 30 golpes em cada camada, distribuídos uniformemente. A última conterá um excesso de concreto; retire-o com régua metálica;
deixe os corpos-de-prova nos moldes, sem sofrer perturbações e em temperatura ambiente por 24 horas;
após este período deve-se identificar os corpos-de-prova e transferi-los para o laboratório, onde serão rompidos para atestar sua resistência.
9. Transporte do Concreto
Compreende o transporte do concreto desde o caminhão betoneira até o destino final (formas), e pode ser feito de dois modos, como descritos a seguir:
CONVENCIONAL
O concreto é transportado até as formas por meio de carrinhos de mão, giricas, caçambas, calhas, gruas, correias transportadoras etc.
BOMBEÁVEL
Neste caso é utilizado um equipamento denominado "bomba de concreto", que transporta o concreto através de uma tubulação metálica desde o caminhão betoneira até a peça a ser concretada, vencendo grandes alturas ou grandes distâncias horizontais.
A bomba de concreto tem capacidade de lançar volumes elevados de concreto em curto espaço de tempo. Enquanto no transporte convencional se atingem 4 a 7 m³ de concreto por hora, com a bomba de concreto se alcançam produções de 35 a 45 m³ por hora.
A utilização de bombas de concreto permite racionalizar mão-de-obra e, ainda, sendo o concreto bombeado mais plástico, necessitará de menor energia de vibração.
Isso se traduz em menores custos para a obra, menor quantidade de equipamentos e grande produtividade.
10. Cuidados na Aplicação
Uma boa concretagem deve garantir que o concreto chegue à fôrma coesa, que preencha todos os seus cantos e armadura e seja adequadamente vibrado.
Este objetivo será atingido se forem observados os seguintes cuidados:
procurar o menor percurso possível para o concreto; no lançamento convencional, as rampas não devem ter inclinação excessiva e os acessos deverão ser planos, de modo a evitar a segregação decorrente do transporte do concreto até a forma; preencher uniformemente a forma, evitando o lançamento em pontos concentrados que possam causar deformações; não lançar o concreto de altura superior a três metros, nem jogá-lo a grande distância com pá para evitar a separação da brita. Quando a altura for muito elevada deve-se utilizar anteparos ou funil; preencher as formas em camadas de, no máximo, 50 cm para se obter um adensamento adequado.
11. Adensamento do Concreto
Uma boa concretagem deve garantir que o concreto chegue à fôrma coesa, que preencha todos os seus cantos e armadura e seja adequadamente vibrado.
Este objetivo será atingido se forem observados os seguintes cuidados:
procurar o menor percurso possível para o concreto; no lançamento convencional, as rampas não devem ter inclinação excessiva e os acessos devera ser planos, de modo a evitar a segregação decorrente do transporte do concreto até a forma; preencher uniformemente a forma, evitando o lançamento em pontos concentrados que possam causar deformações; não lançar o concreto de altura superior a três metros, nem jogá-lo a grande distância com pá para evitar a separação da brita. Quando a altura for muito elevada deve-se utilizar anteparos ou funil; preencher as formas em camadas de, no máximo, 50 cm para se obter um adensamento adequado.
12. Juntas de Concretagem
Se, por algum motivo, a concretagem tiver que ser interrompida, deve-se planejar o local onde ocorrerá a interrupção da mesma.
O concreto novo possui pouca aderência ao já enduecido. Para que haja uma perfeita aderência entre a superfície já concretada (concreto endurecido) e aquela a ser concretada, cuja ligação chamamos de junta de concretagem, devemos observar alguns procedimentos:
deve-se remover toda a nata de cimento (parte vitrificada), por jateamento de abrasivo ou por apicoamento,com posterior lavagem, de modo a deixar aparente a brita, para que haja uma melhor aderência com o concreto a ser lançado; é necessária a interposição de uma camada de argamassa com as mesmas características da que compõe o concreto; as juntas de concretagem devem garantir a resistência aos esforços que podem agir na superficie da junta; deve-se prever a interrupção da concretagem em pontos que facilitem a retomada da concretagem da peça, para que não haja a formação de "nichos" de concretagem, evitando a descontinuidade na vizinhança daquele ponto.
13. Cura do Concreto
Após o endurecimento do concreto, este continua a ganhar resistência, mas para que isto ocorra deve-se iniciar o último, mas não o menos importante, procedimento da fase de concretagem de uma peça de concreto: a cura.
A evaporação prematura da água pode provocar fissuras na superficie do concreto e, ainda, reduzir em até 30% sua resistência.
Podemos então afirmar que quanto mais perfeita e demorada for a cura do concreto tanto melhores serão suas características finais.
Destacamos, abaixo, os métodos mais recomendados para a cura do concreto:
molhar continuamente a superficie do concreto, logo após o endurecimento, durante os 7 primeiros dias; manter uma lâmina d'água sobre a peça concretada, sendo este método limitado a lajes, pisos ou pavimentos; manter a peça umedecida por meio de uma camada de areia úmida, serragem, sacos de aniagem ou tecido de algodão; utilizar membranas de cura, que são produtos químicos aplicados na superficie do concreto que evitam a evaporação precoce da água; deixar o concreto nas fôrmas, mantendo-as molhadas.
14. Retirada de Fôrmas e Escoramentos
As formas e os escoramentos só poderão ser retirados quando o concreto resistir com segurança e sem sofrer deformações, ao seu peso próprio e às cargas atuantes.
De uma forma geral, quando se tratar de concreto convencional, sem a utilização de cimento de alta resistência inicial, deve-se respeitar os seguintes prazos para a retirada das formas e escoramentos:
face lateral da forma : 3 dias faces inferiores, mantendo-se os pontaletes bem encunhados e convenientemente espaçados: 14 dias faces inferiores, sem pontaletes: 21 dias
Os apoios devem ser retirados gradualmente, de modo que a peça entre em carga progressivamente e de forma uniforme.
Deve-se retirar as formas com cuidado, sem choques ou a utilização de ferramentas que danifiquem a superficie do concreto.
15. Resistência do Concreto
Uma vez obedecidas todas as práticas recomendadas neste manual, temos que saber se a resistência especificada em projeto pelo calculista foi atingida. No ensaio de ruptura por compressão, os corpos-de-prova que foram moldados na obra são submetidos a um carregamento uniforme, em prensas especiais, até seu rompimento.
Após a ruptura dos corpos-de-prova, e de posse dos resultados dos ensaios, é realizado o "controle estatístico da resistência do concreto", para certificar a aceitação da estrutura concretada sob o ponto de vista estrutural.
Este controle é de suma importância como testemunho da segurança da estrutura que será futuramente utilizada.
Ao se adquirir o concreto dosado em central, a empresa concreteira garante a qualidade do concreto, segundo as rígidas exigências das normas técnicas brasileiras. Isto é conseguido não só pela garantia da resistência do concreto, mas também por outros procedimentos que são descritos no próximo item.
16. Controle da Qualidade do Concreto
Além do controle da resistência do concreto à compressão, como uma das formas de controle da qualidade, as empresas concreteiras realizam uma série de outros ensaios de qualidade nos materiais que serão utilizados na elaboração do concreto - agregados (pedra e areia), cimento, água e aditivos.
Hoje as concreteiras possuem laboratórios sofisticados de controle de qualidade, e os ensaios são realizados conforme exigências das normas técnicas brasileiras.
O trabalho específico desenvolvido pelas centrais dosadoras, operadas por pessoal técnico especializado, permite o controle de todos os materiais utilizados na dosagem bem como as propriedades exigidas pelo projeto e de acordo com as normas técnicas vigentes.
17. Concreto Impermeável
Uma das propriedades desejadas do concreto impermeável é, obviamente, que ele resista à penetração da água, como por exemplo em caixas d'água, lajes, piscinas, etc.
O caminho para se obter um concreto impermeável começa em um projeto adequado, que evite o fissuramento do concreto quando este estiver sendo solicitado.
O concreto a ser empregado também deve ser cuidadosamente elaborado, devendo ser bem argamassado, com um consumo adequado de cimento (mínimo de 350 kg/m³ ), procurando empregar britas menores (brita o ou brita 1, no máximo). O uso de aditivos é recomendável. O concreto deve ser ainda fácil de trabalhar, de modo a ocupar toda a fôrma sem impedimentos.
O adensamento adequado também contribui para se obter um concreto impermeável, devendo ser executado com vibradores de imersão (não utilize barras de aço para vibrar o concreto).
A cura também deve ser criteriosa, pois irá impedir que o concreto fissure por retração, recomendando-se seu início logo que o concreto comece a endurecer e sua continuidade por pelo menos 7 dias.
18. Concreto Aparente
Quando o concreto for utilizado como material de acabamento, ou seja, sem revestimento, alguns cuidados devem ser observados.
Para se obter acabamento liso deve-se empregar fôrmas de madeira plastificadas ou metálicas, já que estes tipos de fôrma proporcionam menor concentração de bolhas de ar junto à superfície.
Os desmoldantes facilitam a retirada das fôrmas depois que o concreto endureceu, evitando que o concreto "cole" à fôrma. Estes não devem reagir com o cimento, nem causar manchas na superficie do concreto. A camada de desmoldante deve ser uniforme, evitando-se concentração em pontos isolados da fôrma que causam descolamento de pequenas placas da superfície do concreto onde o desmoldante está em excesso.
O emprego de óleo mineral, virgem ou recuperado, pode provocar enferrujamento de fôrmas metálicas.
Outros cuidados dizem respeito à vibração adequada do concreto e a evitar que a armadura fique próxima da superficie. O uso de aditivos plastificantes são altamente recomendáveis neste caso.
O concreto a ser utilizado deve conter uma quantidade adequada de argamassa.
O concreto do tipo bombeável pode ser utilizado para o concreto aparente.
Fonte: Eng. Luiz Carlos Thiers Silva
O Blog do Profissional Técnico de Obra Civil. Construir com economia, segurança e tecnologia utilizando os recursos disponíveis
Mostrando postagens com marcador Concreto. Mostrar todas as postagens
Mostrando postagens com marcador Concreto. Mostrar todas as postagens
quarta-feira, 17 de junho de 2009
Concreto
Dicas de construção - Concreto
Normalmente ignorado em diversas obras, inclusive grandes empreendimentos executados por construtoras de renome, o cobrimento do concreto é um elemento de grande responsabilidade pela saúde das estruturas de concreto armado. O descuido rotineiro com esse item de extrema importância tem resultado ultimamente em diversas obras de recuperação estrutural que, quase sempre, envolvem altas somas em dinheiro.
O concreto, se bem executado, tem por natureza, como uma de suas vantagens, proteger as armaduras da corrosão. Essa proteção baseia-se no impedimento da formação de células eletroquímicas, através da proteção física e proteção química.
Um bom cobrimento das armaduras, com concreto de alta compacidade, sem ninhos e com um perfeito equilíbrio entre seus elementos e homogeneidade garante, por impermeabilidade, a proteção do aço ao ataque de agentes agressivos externos. Esses agentes podem estar contidos na atmosfera, em águas residuais, águas do mar, águas industriais, dejetos orgânicos, etc.
Outra função do cobrimento é a proteção química das armaduras. Em ambiente altamente alcalino, é formada uma capa ou película protetora de caráter passivo na superfície do aço. O cobrimento protege essa capa protetora contra danos mecânicos e, ao mesmo tempo mantém a sua estabilidade.
Recomenda-se, por isso, que o engenheiro projetista especifique adequadamente o cobrimento do concreto armado para o tipo de utilização da estrutura, em concordância com norma brasileira vigente, e que este seja respeitado durante a execução.
Fonte: Eng. Luiz Carlos Thiers Silva
Normalmente ignorado em diversas obras, inclusive grandes empreendimentos executados por construtoras de renome, o cobrimento do concreto é um elemento de grande responsabilidade pela saúde das estruturas de concreto armado. O descuido rotineiro com esse item de extrema importância tem resultado ultimamente em diversas obras de recuperação estrutural que, quase sempre, envolvem altas somas em dinheiro.
O concreto, se bem executado, tem por natureza, como uma de suas vantagens, proteger as armaduras da corrosão. Essa proteção baseia-se no impedimento da formação de células eletroquímicas, através da proteção física e proteção química.
Um bom cobrimento das armaduras, com concreto de alta compacidade, sem ninhos e com um perfeito equilíbrio entre seus elementos e homogeneidade garante, por impermeabilidade, a proteção do aço ao ataque de agentes agressivos externos. Esses agentes podem estar contidos na atmosfera, em águas residuais, águas do mar, águas industriais, dejetos orgânicos, etc.
Outra função do cobrimento é a proteção química das armaduras. Em ambiente altamente alcalino, é formada uma capa ou película protetora de caráter passivo na superfície do aço. O cobrimento protege essa capa protetora contra danos mecânicos e, ao mesmo tempo mantém a sua estabilidade.
Recomenda-se, por isso, que o engenheiro projetista especifique adequadamente o cobrimento do concreto armado para o tipo de utilização da estrutura, em concordância com norma brasileira vigente, e que este seja respeitado durante a execução.
Fonte: Eng. Luiz Carlos Thiers Silva
segunda-feira, 15 de junho de 2009
Dosagem do concreto
PREPARO DO CONCRETO
A qualidade das benfeitorias executadas com concreto não depende apenas das características dos seus componentes. As sete etapas, explicadas a seguir, também contribuem muito para garantir a qualidade e a economia desejadas.
1- Dosagem do concreto
O concreto é uma mistura dos vários componentes, em determinadas proporções, chamadas de dosagem ou traço, na linguagem da construção civil.
O traço varia de acordo com a finalidade de uso e com as condições de aplicação. A tabela seguinte apresenta os traços mais adequados para os principais usos no meio rural. Se nenhum deles se alicar ao seu caso específico, consulte um profissional habilitado.
Atenção:
1) A lata de medida deve ser de 18 litros.
2) As pedras devem ser 1 ou 2.
2- Cálculo estrutural
O traço define a proporção dos componentes do concreto simples. Caso seja utilizado o concreto armado, é preciso definir também a posição, o tipo, a bitola e a quantidade dos vergalhões que vão compor a armadura. Essa determinação chama-se cálculo estrutural e deve ser feita, obrigatoriamente, por um profissiona habilitado.
3- Execução das fôrmas
Como já dito, o concreto é moldável. Por isso, é preciso prever a montagem dos moldes - chamados de fôrmas, na linguagem da construção civil. As fôrmas devem ser muito bem feitas, travadas e escoradas, para que a estrutura de concreto tenha boa qualidade e não ocorram deformações ( só para se ter uma idéia, o peso do concreto é duas vezes e meia maior que o da água).
As fôrmas também devem ser estanques (sem fendas ou buracos) para evitar o vazamento do concreto.
As formas podem ser feitas de diversos materiais: madeira, alumínio, fibra de vidro, aço, plástico.
As fôrmas são compostas de 2 elementos:
- o caixão da fôrma, que contém o concreto e, portanto, fica em contato com ele;
- a estruturação da fôrma, que evita a deformação e resiste ao peso do concreto.
O caixão da fôrma é feito com chapas de madeira compensada. Na estruturação podem ser usadas peças de madeira serrada ou madeira bruta.
Quanto ao acabamento da superfície, existem dois tipos de chapas no mercado: plastificadas e resinadas.
O aproveitamento médio das plastificadas é de 15 vezes, enquanto o das resinadas é de 4 a 5 vezes.
O travamento e o escoramento das fôrmas requerem muito cuidado. Dependendo do tamanho do vão ou do peso do concreto a ser suportado, é necessário usar peás mais robustas de madeira serrada, como tábuas, vigas ou até pranchões. As madeiras brutas podem substituir as serradas no escoramento e, eventualmente, no travamento. Mas é desaconselhável o seu uso em outras funções, como o encaibramento das lajes, por exemplo. O travamento, o alinhamento, o prumo e o nivelamento das fôrmas devem ser conferidos antes da concretagem, para evitar deformações no concreto.
As ferramenta necessárias para a execução de uma fôrma são : serrote, martelo de carpinteiro, prumo, linha, maangueira de nível e, eventualmente, uma bancada para "bater"as fôrmas.
4- Execução da armadura
A execução da armadura compreende as seguintes operações: corte, dobramento, amarração, posicionamento, conferência.
As principais peças de concreto armado das benfeitorias de pequeno porte têm formato ou função de : fundações, vigas, pilares, lajes.
A armadura das fundações das obras de pequeno porte consiste, em geral, de dois ou três vergalhões.
Os pilares e as vigas têm armadura composta de vergalhões longitudinais e estribos.
Estes, mantém os vergalhões longitudinais na posição correta e ajudam o conjunto a aguentar esforços de torção e flexão. As extremidades dos vergalhões longitudinais devem ser dobradas em forma de gancho, para garantir sua ancoragem ao concreto.
As lajes concretadas no local têm vergalhões nos sentidos de comprimento e da largura,formando uma tela.
O conjunto de pilares, vigas e lages é submetido ainda a outros esforços. Por isso, o cálculo estrutural determina também a colocação de uma armadura complementar, chamada de ferro negativo.
Em geral, as armaduras são montadas no local da obra, sobre cavaletes onde os vergalhões são amarrados uns aos outros com arame cozido.
Emendas de vergalhões devem ser evitadas. Caso ejam necessárias, devem ficar desencontradas (ou desalinhadas). O transpasse (ou trespasse) da emenda deve ter um comprimento de oitenta vezes o diâmetro do vergalhão.
Quando são usadas telas soldadas, uma tela deve cobrir 2 malhas da outra.
Tanto os vergalhões como as telas devem ser firmemente amarrados nas emendas.
O concreto resiste bem ao tempo mas a armadura pode sofrer corrosão se não ficar bem protegida por uma camada de cobrimento de, no mínimo, 1 cm de concreto. Para garantir que a armadura fique a essa distância mínima da superfície, são usados espaçadores (pequenas peças de argamassa de cimento e areia, fixadas na armadura).
As ferramentas necessária para a confecção de armaduras são: tesourão, serra de arco, Torquês, alavanca para dobrar, bancada com pinos.
5- Mistura do concreto
O concreto pode ser misturado de três modos: manualmente, em betoneiras, em usina ( central de concreto ou concreteira).
- Mistura manual do concreto:
a) Espalhe a areia formando uma camada de uns 15 cm;
b) Sobre a areia, coloque o cimento;
c) Com uma pá ou enxada mexa a areia e o cimento até formar uma mistura bem uniforme;
d) Espalhe a mistura formando uma camada de 15cm a 20 cm;
e) Coloque a pedra sobre essa camada, misturando tudo muito bem;
f) Faça um monte com um buraco (coroa) no meio;
g) Adicione e misture a água aos poucos, evitando que escorra.
É muito importante que a quantidade de água da mistura esteja correta. Tanto o excesso quanto a falta são prejudiciais ao concreto. Se a mistura ficar com muita água, a resistência do concreto pode diminuir bastante, porque os componenentes, em geral, se separam. Ao contrário, se a mistura ficar seca, ele será difícil de adensar. Além disso, a peça concretaa ficará cheia de buracos, com a aparência ruim e com baixa resistência.
A mistura do concreto deve ser uma tentativa de acertar o traço a ser adotado nas misturas seguintes com o mesmo material. Sempre que a areia, a pedra ou o cimento mudar, será necessário ajustar o traço novamente.
Caso seja difícil saber, pela observação visual, se a quantidade de água da mistura está correta, a solução é alisar a supefície da mistura com uma colher de pedreiro para ver o que acontece:
a) Se a superfície alisada ficar úmida, mas não escorrer água, a quantidade de água está certa;
b) Se escorrer há excesso de água. Isso deve ser imediatamente corrigido: coloque mais um pouco de pedra e areia na mistura e mexa tudo de novo, até não escorrer mais água;
c) Se a superfície alisada nem ficar úmida, é sinal de que falta água. Nesse caso, continue misturando a massa, pois, em geral, com mais algumas mexidas o concreto costuma ficar mais mole. Se a mistura ainda ficar muito seca, adicione cimento e água, na poção de cinco partes de cimento para cada três de água. Para isso, use um recipiente pequeno (por exemplo, uma lata limpa de óleo de cozinha). Nunca adicione apenas água na mistura, pois isso diminui muito a resistência do concreto.
- Concreto misturado em betoneira
A betoneira é uma máquina que agiliza a mistura do concreto.
a) Coloque a pedra na betoneira;
b) Adicione metade de água e misture por um minuto;
c) Ponha o cimento;
d) Por último, ponha a areia e o resto da água.
A betoneira precisa estar limpa (livre de pó, água suja e restos da última utilização) antes de ser usada. Os materiais devem ser colocados com a betoneira girando e no menor espaço de tempo possível. Após a colocação de todos os componentes do concreto, a betoneira ainda deve girar por, no mínimo, 3 minutos.
Para verificar se a quantidade de água está correta, pode ser feirto o mesmo teste da colher de pedreiro, já descrito na mistura manual do concreto. Se houver necessidade, o ajuste da quantidade de água deve ser feito da mesma forma.
Existem no mercado betoneiras com diferentes capacidades, de produção de concreto. A maioria é movida a energia elétrica. Essas máquinas podem ser alugadas ou compradas dos seus fabricantes ou distribuidores.
As ferramentas necessárias para a mistura do concreto são: enxada, pá, carrinho de mão, betoneira, lata de 18 litros, colher de pedreiro.
- Concreto misturado em usina (central de concreto ou concreteira)
O concreto também pode ser comprado pronto, já misturado no traço desejado e entregue no local da obra por caminhões-betoneira. Esse tipo de fornecimento só é viável para quantidades acima de 3 metros cúbicos e para obras não muito distantes das usinas ou concreteiras, por questão de custo.
6- Concretagem
A concretagem abrange o transporte do concreto recém misturado, o seu lançamento nas fôrmas e o seu adensamento dentro delas. A concretagem deve ser feita no máximo uma hora após a mistura ficar pronta. Nessa etapa é importante a presença de um profissional experiente.
O transporte pode ser feito em latas ou carrinho de mão, sem agitar muito a mistura,
para evitar a separação dos componente.
As fôrmas devem ser limpas antes da concretagem. Quaiquer buracos ou fendas que possam deixar o concreto vazar precisam ser fechados. Em seguida as fôrmas têm de ser molhadas para que não absorvam a água do concreto. Esse não deve ser lançado de grande altura, para evitar que os componentes se separem na queda. o certo é despejar o concreto da altura da borda da fôrma.
A concretagem nunca deve parar pela metade, para evitar emendas, que ficarão visíveis depois da desforma.
O concreto deve ser adensado em camadas, à medida que é lançado nas fôrmas. Isso pode ser feito manualmente, com um soquete (haste feita de madeira ou barra de aço) ou com a ajuda de vibradores elétricos. O adensamento é necessário para que o concreto preencha toda a fôrma, sem deixar vazios ou bolhas. Quanto mais adensado (compactado) for o concreto, maior será sua resistência e durabilidade.
As ferramentas necessárias para a concretagem são: pá, enxada, carrinho de mão, lata de 18 litros e colher de pedreiro.
7- Cura e desforma do concreto
Cura é a fase de secagem do concreto, na linguagem da contrução civil. Ela é importantíssima: se não for feita de modo correto, o concreto não terá a resistência e a durabilidade desejadas.
Ao contrário do que se possa pensa, para uma boa cura não basta deixar o concreto simplesmente secar ao tempo. O sol e o vento secam o concreto depressa demais. Na verdade, ele deve ser mantido úmido por uma semana. Isso pode ser feito regando o concreto pelo menos uma vez por dia ou cobrindo a sua superfície com sacaria ou capim molhados.
Mas cuidado: o concreto fresco não pode ficar encharcado nas orimeiras seis horas aós a mistura, quando ainda está mole. Caso haja o risco de cair uma chuva forte após o término da concretagem de uma peça de grande superfície, (uma laje ou um piso) o concreto fresco deve imediatamente ser coberto com uma lona plástica.
A desforma, ou seja, a retirada das fôrmas, deve ser feita depois que o concreto atingir uma boa resistência, geralmente três dias após a concretagem.
Primeiro, são retiradas as peças laterais, com cuidado, evitando choques ou pancadas, para não estragar as fôrmas e para não transmitir vibrações ou esforços ao concreto. O escoramento das fôrmas de lajes ou vigas só deve ser retirado 3 semanas após a concretagem.
As ferramenta necessárias para a desforma são: Martelo de carpinteiro, pé-de-cabra e serrote.
A qualidade das benfeitorias executadas com concreto não depende apenas das características dos seus componentes. As sete etapas, explicadas a seguir, também contribuem muito para garantir a qualidade e a economia desejadas.
1- Dosagem do concreto
O concreto é uma mistura dos vários componentes, em determinadas proporções, chamadas de dosagem ou traço, na linguagem da construção civil.
O traço varia de acordo com a finalidade de uso e com as condições de aplicação. A tabela seguinte apresenta os traços mais adequados para os principais usos no meio rural. Se nenhum deles se alicar ao seu caso específico, consulte um profissional habilitado.
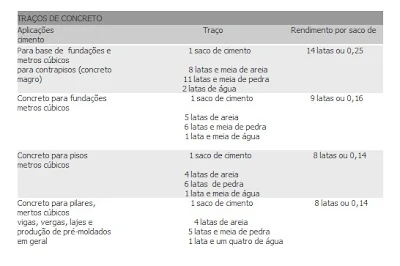
Atenção:
1) A lata de medida deve ser de 18 litros.
2) As pedras devem ser 1 ou 2.
2- Cálculo estrutural
O traço define a proporção dos componentes do concreto simples. Caso seja utilizado o concreto armado, é preciso definir também a posição, o tipo, a bitola e a quantidade dos vergalhões que vão compor a armadura. Essa determinação chama-se cálculo estrutural e deve ser feita, obrigatoriamente, por um profissiona habilitado.
3- Execução das fôrmas
Como já dito, o concreto é moldável. Por isso, é preciso prever a montagem dos moldes - chamados de fôrmas, na linguagem da construção civil. As fôrmas devem ser muito bem feitas, travadas e escoradas, para que a estrutura de concreto tenha boa qualidade e não ocorram deformações ( só para se ter uma idéia, o peso do concreto é duas vezes e meia maior que o da água).
As fôrmas também devem ser estanques (sem fendas ou buracos) para evitar o vazamento do concreto.
As formas podem ser feitas de diversos materiais: madeira, alumínio, fibra de vidro, aço, plástico.
As fôrmas são compostas de 2 elementos:
- o caixão da fôrma, que contém o concreto e, portanto, fica em contato com ele;
- a estruturação da fôrma, que evita a deformação e resiste ao peso do concreto.
O caixão da fôrma é feito com chapas de madeira compensada. Na estruturação podem ser usadas peças de madeira serrada ou madeira bruta.
Quanto ao acabamento da superfície, existem dois tipos de chapas no mercado: plastificadas e resinadas.
O aproveitamento médio das plastificadas é de 15 vezes, enquanto o das resinadas é de 4 a 5 vezes.
O travamento e o escoramento das fôrmas requerem muito cuidado. Dependendo do tamanho do vão ou do peso do concreto a ser suportado, é necessário usar peás mais robustas de madeira serrada, como tábuas, vigas ou até pranchões. As madeiras brutas podem substituir as serradas no escoramento e, eventualmente, no travamento. Mas é desaconselhável o seu uso em outras funções, como o encaibramento das lajes, por exemplo. O travamento, o alinhamento, o prumo e o nivelamento das fôrmas devem ser conferidos antes da concretagem, para evitar deformações no concreto.
As ferramenta necessárias para a execução de uma fôrma são : serrote, martelo de carpinteiro, prumo, linha, maangueira de nível e, eventualmente, uma bancada para "bater"as fôrmas.
4- Execução da armadura
A execução da armadura compreende as seguintes operações: corte, dobramento, amarração, posicionamento, conferência.
As principais peças de concreto armado das benfeitorias de pequeno porte têm formato ou função de : fundações, vigas, pilares, lajes.
A armadura das fundações das obras de pequeno porte consiste, em geral, de dois ou três vergalhões.
Os pilares e as vigas têm armadura composta de vergalhões longitudinais e estribos.
Estes, mantém os vergalhões longitudinais na posição correta e ajudam o conjunto a aguentar esforços de torção e flexão. As extremidades dos vergalhões longitudinais devem ser dobradas em forma de gancho, para garantir sua ancoragem ao concreto.
As lajes concretadas no local têm vergalhões nos sentidos de comprimento e da largura,formando uma tela.
O conjunto de pilares, vigas e lages é submetido ainda a outros esforços. Por isso, o cálculo estrutural determina também a colocação de uma armadura complementar, chamada de ferro negativo.
Em geral, as armaduras são montadas no local da obra, sobre cavaletes onde os vergalhões são amarrados uns aos outros com arame cozido.
Emendas de vergalhões devem ser evitadas. Caso ejam necessárias, devem ficar desencontradas (ou desalinhadas). O transpasse (ou trespasse) da emenda deve ter um comprimento de oitenta vezes o diâmetro do vergalhão.
Quando são usadas telas soldadas, uma tela deve cobrir 2 malhas da outra.
Tanto os vergalhões como as telas devem ser firmemente amarrados nas emendas.
O concreto resiste bem ao tempo mas a armadura pode sofrer corrosão se não ficar bem protegida por uma camada de cobrimento de, no mínimo, 1 cm de concreto. Para garantir que a armadura fique a essa distância mínima da superfície, são usados espaçadores (pequenas peças de argamassa de cimento e areia, fixadas na armadura).
As ferramentas necessária para a confecção de armaduras são: tesourão, serra de arco, Torquês, alavanca para dobrar, bancada com pinos.
5- Mistura do concreto
O concreto pode ser misturado de três modos: manualmente, em betoneiras, em usina ( central de concreto ou concreteira).
- Mistura manual do concreto:
a) Espalhe a areia formando uma camada de uns 15 cm;
b) Sobre a areia, coloque o cimento;
c) Com uma pá ou enxada mexa a areia e o cimento até formar uma mistura bem uniforme;
d) Espalhe a mistura formando uma camada de 15cm a 20 cm;
e) Coloque a pedra sobre essa camada, misturando tudo muito bem;
f) Faça um monte com um buraco (coroa) no meio;
g) Adicione e misture a água aos poucos, evitando que escorra.
É muito importante que a quantidade de água da mistura esteja correta. Tanto o excesso quanto a falta são prejudiciais ao concreto. Se a mistura ficar com muita água, a resistência do concreto pode diminuir bastante, porque os componenentes, em geral, se separam. Ao contrário, se a mistura ficar seca, ele será difícil de adensar. Além disso, a peça concretaa ficará cheia de buracos, com a aparência ruim e com baixa resistência.
A mistura do concreto deve ser uma tentativa de acertar o traço a ser adotado nas misturas seguintes com o mesmo material. Sempre que a areia, a pedra ou o cimento mudar, será necessário ajustar o traço novamente.
Caso seja difícil saber, pela observação visual, se a quantidade de água da mistura está correta, a solução é alisar a supefície da mistura com uma colher de pedreiro para ver o que acontece:
a) Se a superfície alisada ficar úmida, mas não escorrer água, a quantidade de água está certa;
b) Se escorrer há excesso de água. Isso deve ser imediatamente corrigido: coloque mais um pouco de pedra e areia na mistura e mexa tudo de novo, até não escorrer mais água;
c) Se a superfície alisada nem ficar úmida, é sinal de que falta água. Nesse caso, continue misturando a massa, pois, em geral, com mais algumas mexidas o concreto costuma ficar mais mole. Se a mistura ainda ficar muito seca, adicione cimento e água, na poção de cinco partes de cimento para cada três de água. Para isso, use um recipiente pequeno (por exemplo, uma lata limpa de óleo de cozinha). Nunca adicione apenas água na mistura, pois isso diminui muito a resistência do concreto.
- Concreto misturado em betoneira
A betoneira é uma máquina que agiliza a mistura do concreto.
a) Coloque a pedra na betoneira;
b) Adicione metade de água e misture por um minuto;
c) Ponha o cimento;
d) Por último, ponha a areia e o resto da água.
A betoneira precisa estar limpa (livre de pó, água suja e restos da última utilização) antes de ser usada. Os materiais devem ser colocados com a betoneira girando e no menor espaço de tempo possível. Após a colocação de todos os componentes do concreto, a betoneira ainda deve girar por, no mínimo, 3 minutos.
Para verificar se a quantidade de água está correta, pode ser feirto o mesmo teste da colher de pedreiro, já descrito na mistura manual do concreto. Se houver necessidade, o ajuste da quantidade de água deve ser feito da mesma forma.
Existem no mercado betoneiras com diferentes capacidades, de produção de concreto. A maioria é movida a energia elétrica. Essas máquinas podem ser alugadas ou compradas dos seus fabricantes ou distribuidores.
As ferramentas necessárias para a mistura do concreto são: enxada, pá, carrinho de mão, betoneira, lata de 18 litros, colher de pedreiro.
- Concreto misturado em usina (central de concreto ou concreteira)
O concreto também pode ser comprado pronto, já misturado no traço desejado e entregue no local da obra por caminhões-betoneira. Esse tipo de fornecimento só é viável para quantidades acima de 3 metros cúbicos e para obras não muito distantes das usinas ou concreteiras, por questão de custo.
6- Concretagem
A concretagem abrange o transporte do concreto recém misturado, o seu lançamento nas fôrmas e o seu adensamento dentro delas. A concretagem deve ser feita no máximo uma hora após a mistura ficar pronta. Nessa etapa é importante a presença de um profissional experiente.
O transporte pode ser feito em latas ou carrinho de mão, sem agitar muito a mistura,
para evitar a separação dos componente.
As fôrmas devem ser limpas antes da concretagem. Quaiquer buracos ou fendas que possam deixar o concreto vazar precisam ser fechados. Em seguida as fôrmas têm de ser molhadas para que não absorvam a água do concreto. Esse não deve ser lançado de grande altura, para evitar que os componentes se separem na queda. o certo é despejar o concreto da altura da borda da fôrma.
A concretagem nunca deve parar pela metade, para evitar emendas, que ficarão visíveis depois da desforma.
O concreto deve ser adensado em camadas, à medida que é lançado nas fôrmas. Isso pode ser feito manualmente, com um soquete (haste feita de madeira ou barra de aço) ou com a ajuda de vibradores elétricos. O adensamento é necessário para que o concreto preencha toda a fôrma, sem deixar vazios ou bolhas. Quanto mais adensado (compactado) for o concreto, maior será sua resistência e durabilidade.
As ferramentas necessárias para a concretagem são: pá, enxada, carrinho de mão, lata de 18 litros e colher de pedreiro.
7- Cura e desforma do concreto
Cura é a fase de secagem do concreto, na linguagem da contrução civil. Ela é importantíssima: se não for feita de modo correto, o concreto não terá a resistência e a durabilidade desejadas.
Ao contrário do que se possa pensa, para uma boa cura não basta deixar o concreto simplesmente secar ao tempo. O sol e o vento secam o concreto depressa demais. Na verdade, ele deve ser mantido úmido por uma semana. Isso pode ser feito regando o concreto pelo menos uma vez por dia ou cobrindo a sua superfície com sacaria ou capim molhados.
Mas cuidado: o concreto fresco não pode ficar encharcado nas orimeiras seis horas aós a mistura, quando ainda está mole. Caso haja o risco de cair uma chuva forte após o término da concretagem de uma peça de grande superfície, (uma laje ou um piso) o concreto fresco deve imediatamente ser coberto com uma lona plástica.
A desforma, ou seja, a retirada das fôrmas, deve ser feita depois que o concreto atingir uma boa resistência, geralmente três dias após a concretagem.
Primeiro, são retiradas as peças laterais, com cuidado, evitando choques ou pancadas, para não estragar as fôrmas e para não transmitir vibrações ou esforços ao concreto. O escoramento das fôrmas de lajes ou vigas só deve ser retirado 3 semanas após a concretagem.
As ferramenta necessárias para a desforma são: Martelo de carpinteiro, pé-de-cabra e serrote.
Concreto e componentes
CONCRETO
O Concreto é uma mistura, em determinadas proporções, de quatro componentes básicos: cimento, pedra, areia e água.
Tipos de concreto: simples, armado e magro.
O concreto simples é preparado com os 4 componentes básicos e tem grande resistência aos esforços de compressão, mas baixa resistência aos esforços de tração.
Já o concreto armado tem elevada resistência tanto aos esforços de tração como aos de compressão, mas para isso precisa de um quinto componente: armadura ou ferro.
O concreto magro é na verdade um concreto simples com menos cimento. Ele é mais econômico mas só pode ser usado em partes da construção que não exijam tanta resistência e impermeabilidade.
COMPONENTES DO CONCRETO
1.Cimento
As matérias primas do cimento são calcário, argila, gesso e outros materiais denominados adições. A sua fabricação exige grandes e complexas instalações industriais, como um possante forno giratório que chega a atingir temperaturas próximas a 1500ºC.
No mercado existem diverso tipos de cimento. A diferença entre eles está na composição, mas todos atendem às exigências das Normas Técnicas Brasileiras. Cada tipo tem o nome e a sigla correspondente estampada na embalagem, para facilitar a identificação. Os tipos de cimento adequados aos usos gerais no meio rural são os seguintes:
NOME SIGLA (estampada na embalagem)
CIMENTO PORTLAND comum com adição CP I-S-32
CIMENTO PORTLAND composto com escória CP II-E-32
CIMENTO PORTLAND composto com pozolana CP II-Z-32
CIMENTO PORTLAND composto com filer CP II-F-32
CIMENTO PORTLAND de alto forno CP III-32
CIMENTO PORTLAND pozolânico CP IV-32
Existem ainda outros tipos de cimento para usos específicos.
Em sua embalagem original - sacos de 50 kg - o cimento pode ser armazenado por cerca de 3 meses, desde que o local seja fechado coberto e seco. Além disso, o cimento deve ser estocado sobre estrados de madeira, em pilhas de 10 sacos, no máximo.
2. Pedra
A pedra utilizada no concreto pode ser de dois tipos:
- seixo rolado de rios, cascalho ou pedregulho;
- pedra britada ou brita.
Os seixos rolados são encontrados na natureza. A pedra britada é obtida pela britagem mecânica de deterninadas rochas duras.
Independentemente da origem, o tamanho das pedras varia muito e tem influência na qualidade do concreto. Por isso, as pedras são classificadas por tamanhos medidos em peneiras (pela abertura da malha). As
Normas Técnicas brasileiras estabelecem 6 tamanhos:
TAMANHO DAS PEDRAS
Pedra zero (ou pedrisco) 4,8mm a 9,5mm
Pedra1 9,5mm a 19mm
Pedra2 19mm a 25mm
Pedra3 25mm a 38mm
Pedra4 38mm a 76mm
Pedra-de-mão
O concreto das benfeitorias rurais pode ser feito com pedras 1 ou 2, as mais encontradas no comércio de materiais de construção.
Se forem utilizados seixos rolados, cascalho ou pedregulho, das propriedades, convém classificar esse material antes de seu uso. A forma mais simples, porém menos precisa, de fazer isso é apanhar um punhado de pedras do monte a ser usado e medir a maior dimensão de cada uma com uma régua milimitrada. A maioria das pedras medidas deverá se enquadrar da faixa de pedra 1 (9,5mm a 19mm) e pedra 2 (19mm a 25mm).
Caso o material disponível não esteja de acordo com essas medidas, consulte um proffisional especializado a respeito.
Tanto os seixos rolados como a pedra britada devem estar limpos antes de seu uso. O pó de britagem, o barro da jazida, galhos, folhas, raízes, devem ser retirados à mão ou por lavagem.
3-Areia
A areia utilizada no concreto é obtida em leitos e margens de rios, ou em portos e bancos de areia.
A areia deve ter grãos duros. E, assim como a pedra, ela também precisa estar limpa e livre de torrões de barro, galhos, folhas e raízes antes de ser usada.
As Normas Técnicas Brasileiras classificam a areia, segundo o tamanho de seus grãos, em: muito fina, fina, média, grossa.
Mas isso só tem importância em obras de maior porte. Nesses casos, é necessário consultar um profissional especializado, pois essa classificação só pode ser feita, com precisão, em laboratório.
4- Água
A água a ser utilizada no concreto deve ser limpa - sem barro, óleo, galhos, folhas e raízes. Em outras palavras, água boa para o concreto é água de beber. Nunca use água servida ( de esgoto humano ou animal, de cozinha, de fábricas, etc.) no preparo do concreto.
5- Armadura
A armadura é conposta de barras de aço, também chamadas de ferro de construção ou vergalhões. Eles têm a propriedade de se integrar ao concreto e de apresentar elevada resistência à tração. Por isso, são colocados nas partes da peça de concreto que vão sofrer esse esforço. Por exemplo, numa viga apoiada nas extremidades, a parte de cima sofre compressão e a de baixo, tração. Nesse caso, os vergalhões devem ficar na parte debaixo das vigas.
Os vergalhões que compõem a armadura são amarrados uns aos outros com arame recozido.
Existem também armaduras pré-fabricadas, que ja vêm com os vergalhões unidos entre si: são as telas soldadas, que servem de armadura para lajes e pisos.
A maioria dos vergalhões tem saliências na superfície.
As Normas Técnicas Brasileiras classificam os vergalhões para concreto de acordo com a sua resistência e padronizam as bitolas. Há 3 categorias no mercado: aço CA 25, aço CA 50, aço CA 60.
Os números 25, 50 e 60 referem-se á resistência do aço : quanto maior o número, mais resistente será o vergalhão.
Os vergalhões são vendidos em barras retas ou dobradas, com 10m a 12m de comprimento. Eles são cortados e dobrados no formato necessário, no próprio local da obra. O uso de telas soldadas em lajes e pisos reduz a mão-de-obra e elimina as perdas do método de montagem da armadura no local da obra ( pontas cortadas que sobram).
Prefira marcas de vergalhões fabricados em usinas siderúrgicas que tenham um rigoroso controle de qualidade e que respeitem as exigências das Normas Técnicas Brasileiras
O Concreto é uma mistura, em determinadas proporções, de quatro componentes básicos: cimento, pedra, areia e água.
Tipos de concreto: simples, armado e magro.
O concreto simples é preparado com os 4 componentes básicos e tem grande resistência aos esforços de compressão, mas baixa resistência aos esforços de tração.
Já o concreto armado tem elevada resistência tanto aos esforços de tração como aos de compressão, mas para isso precisa de um quinto componente: armadura ou ferro.
O concreto magro é na verdade um concreto simples com menos cimento. Ele é mais econômico mas só pode ser usado em partes da construção que não exijam tanta resistência e impermeabilidade.
COMPONENTES DO CONCRETO
1.Cimento
As matérias primas do cimento são calcário, argila, gesso e outros materiais denominados adições. A sua fabricação exige grandes e complexas instalações industriais, como um possante forno giratório que chega a atingir temperaturas próximas a 1500ºC.
No mercado existem diverso tipos de cimento. A diferença entre eles está na composição, mas todos atendem às exigências das Normas Técnicas Brasileiras. Cada tipo tem o nome e a sigla correspondente estampada na embalagem, para facilitar a identificação. Os tipos de cimento adequados aos usos gerais no meio rural são os seguintes:
NOME SIGLA (estampada na embalagem)
CIMENTO PORTLAND comum com adição CP I-S-32
CIMENTO PORTLAND composto com escória CP II-E-32
CIMENTO PORTLAND composto com pozolana CP II-Z-32
CIMENTO PORTLAND composto com filer CP II-F-32
CIMENTO PORTLAND de alto forno CP III-32
CIMENTO PORTLAND pozolânico CP IV-32
Existem ainda outros tipos de cimento para usos específicos.
Em sua embalagem original - sacos de 50 kg - o cimento pode ser armazenado por cerca de 3 meses, desde que o local seja fechado coberto e seco. Além disso, o cimento deve ser estocado sobre estrados de madeira, em pilhas de 10 sacos, no máximo.
2. Pedra
A pedra utilizada no concreto pode ser de dois tipos:
- seixo rolado de rios, cascalho ou pedregulho;
- pedra britada ou brita.
Os seixos rolados são encontrados na natureza. A pedra britada é obtida pela britagem mecânica de deterninadas rochas duras.
Independentemente da origem, o tamanho das pedras varia muito e tem influência na qualidade do concreto. Por isso, as pedras são classificadas por tamanhos medidos em peneiras (pela abertura da malha). As
Normas Técnicas brasileiras estabelecem 6 tamanhos:
TAMANHO DAS PEDRAS
Pedra zero (ou pedrisco) 4,8mm a 9,5mm
Pedra1 9,5mm a 19mm
Pedra2 19mm a 25mm
Pedra3 25mm a 38mm
Pedra4 38mm a 76mm
Pedra-de-mão
O concreto das benfeitorias rurais pode ser feito com pedras 1 ou 2, as mais encontradas no comércio de materiais de construção.
Se forem utilizados seixos rolados, cascalho ou pedregulho, das propriedades, convém classificar esse material antes de seu uso. A forma mais simples, porém menos precisa, de fazer isso é apanhar um punhado de pedras do monte a ser usado e medir a maior dimensão de cada uma com uma régua milimitrada. A maioria das pedras medidas deverá se enquadrar da faixa de pedra 1 (9,5mm a 19mm) e pedra 2 (19mm a 25mm).
Caso o material disponível não esteja de acordo com essas medidas, consulte um proffisional especializado a respeito.
Tanto os seixos rolados como a pedra britada devem estar limpos antes de seu uso. O pó de britagem, o barro da jazida, galhos, folhas, raízes, devem ser retirados à mão ou por lavagem.
3-Areia
A areia utilizada no concreto é obtida em leitos e margens de rios, ou em portos e bancos de areia.
A areia deve ter grãos duros. E, assim como a pedra, ela também precisa estar limpa e livre de torrões de barro, galhos, folhas e raízes antes de ser usada.
As Normas Técnicas Brasileiras classificam a areia, segundo o tamanho de seus grãos, em: muito fina, fina, média, grossa.
Mas isso só tem importância em obras de maior porte. Nesses casos, é necessário consultar um profissional especializado, pois essa classificação só pode ser feita, com precisão, em laboratório.
4- Água
A água a ser utilizada no concreto deve ser limpa - sem barro, óleo, galhos, folhas e raízes. Em outras palavras, água boa para o concreto é água de beber. Nunca use água servida ( de esgoto humano ou animal, de cozinha, de fábricas, etc.) no preparo do concreto.
5- Armadura
A armadura é conposta de barras de aço, também chamadas de ferro de construção ou vergalhões. Eles têm a propriedade de se integrar ao concreto e de apresentar elevada resistência à tração. Por isso, são colocados nas partes da peça de concreto que vão sofrer esse esforço. Por exemplo, numa viga apoiada nas extremidades, a parte de cima sofre compressão e a de baixo, tração. Nesse caso, os vergalhões devem ficar na parte debaixo das vigas.
Os vergalhões que compõem a armadura são amarrados uns aos outros com arame recozido.
Existem também armaduras pré-fabricadas, que ja vêm com os vergalhões unidos entre si: são as telas soldadas, que servem de armadura para lajes e pisos.
A maioria dos vergalhões tem saliências na superfície.
As Normas Técnicas Brasileiras classificam os vergalhões para concreto de acordo com a sua resistência e padronizam as bitolas. Há 3 categorias no mercado: aço CA 25, aço CA 50, aço CA 60.
Os números 25, 50 e 60 referem-se á resistência do aço : quanto maior o número, mais resistente será o vergalhão.
Os vergalhões são vendidos em barras retas ou dobradas, com 10m a 12m de comprimento. Eles são cortados e dobrados no formato necessário, no próprio local da obra. O uso de telas soldadas em lajes e pisos reduz a mão-de-obra e elimina as perdas do método de montagem da armadura no local da obra ( pontas cortadas que sobram).
Prefira marcas de vergalhões fabricados em usinas siderúrgicas que tenham um rigoroso controle de qualidade e que respeitem as exigências das Normas Técnicas Brasileiras
Assinar:
Postagens (Atom)